DFM Issues Affecting PCB Manufacturing
In the process of printed circuit board (PCB) manufacturing, design for manufacturability (DFM) is an important part to ensure that products can be produced efficiently and economically. If DFM issues are ignored during the design stage, it will lead to manufacturing difficulties, increased costs, and even quality problems. The following are some common DFM issues that affect PCB manufacturing and solutions:
1. Too high wiring density
Problem:
Too dense wiring can cause signal interference (such as crosstalk and impedance mismatch).
Uneven etching during the manufacturing process may cause line breakage or short circuits.
Too small spacing between wiring may exceed the factory's minimum production capacity.
Solution:
Ensure that the wiring spacing and width meet the manufacturer's technical capabilities (for example, minimum line width and minimum spacing).
Use a higher number of PCB layers when designing to disperse the wiring density.
Communicate with the manufacturer in advance to ensure that the design parameters meet its production capabilities.
2. Aperture and via design issues
Problem:
Via size is too small, which increases the difficulty of drilling and plating.
Insufficient hole wall plating thickness may cause poor electrical connections.
Blind or buried vias are complex to design and increase manufacturing costs.
Solution suggestions:
Avoid unnecessary micro vias (such as micro blind and buried vias) unless absolutely necessary.
Ensure that the via size meets the minimum aperture requirements provided by the manufacturer.
If a large number of blind/buried vias are required in the design, make sure to negotiate with the manufacturer to optimize the process.
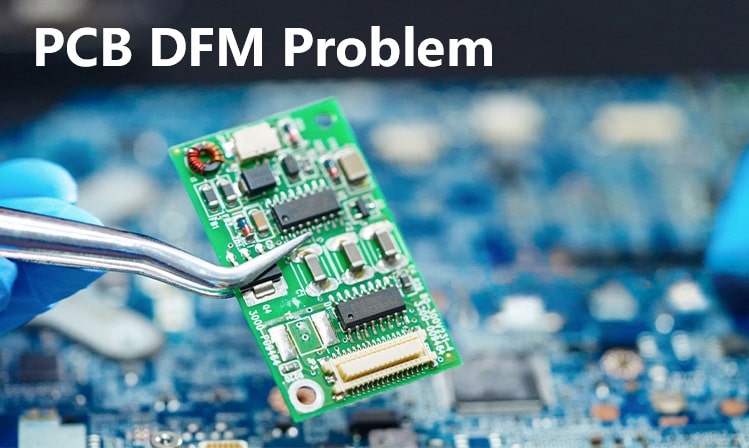
3. Pad and hole design issuesProblem:Insufficient pad size may lead to poor soldering.
Misalignment of pads with holes may affect the soldering reliability of components.
Irregular pads may cause thermal expansion and contraction, resulting in cracking of solder joints.
Solution suggestions:The pad design should meet standard sizes and leave enough space for the soldering process.
Ensure that the pad is aligned with the center of the via.
Add thermal buffer pads under heat-sensitive components to avoid soldering problems caused by thermal stress.
4. Stacking structure and impedance control issuesProblem:
Improper stacking structure design can lead to signal integrity issues.
Routing without impedance control considerations may cause signal distortion, especially in high-speed signal transmission.
Solution suggestions:
Based on the signal type and operating frequency, reasonably design the stacking structure (such as the arrangement of signal layer, ground layer and power layer).
Use differential pair routing and impedance matching design to ensure signal integrity.
Confirm material parameters (such as dielectric constant, copper foil thickness) with the manufacturer to achieve precise impedance control.
5. Copper foil thickness and thermal management issuesProblem:For high current routing, insufficient copper foil thickness may cause overheating or damage.
Improper thermal design may cause PCB overheating, affecting component performance and life.
Solution suggestions:Choose appropriate copper foil thickness (such as 1oz, 2oz, etc.) according to current requirements.
Use appropriate copper filling or increase routing width on high current routing.
Add heat dissipation holes, thermal pads or thermal vias to improve thermal management.
6. Component layout issuesProblem:Components are too dense, which may cause short circuits or other defects during welding.
High heat components close to sensitive components may cause unstable performance.
Improperly positioned components will increase the difficulty of testing and repair.
Solution suggestions:Follow the minimum spacing requirements between components during layout.
Keep high-heat components away from sensitive components and design heat dissipation paths for them.
Optimize component layout for subsequent testing and repair.
7. Silkscreen errors or irregularitiesProblem:The silkscreen mark is blurred or the font is too small, which is not conducive to component identification and assembly.
The silkscreen covers the pad or via, affecting welding and electrical performance.
Solution suggestion:Use clear and easy-to-read silkscreen text and avoid too small fonts.
Ensure that the silkscreen mark does not cover the pad and via area.
8. Board selection problemProblem:Using unsuitable materials (such as FR-4 cannot meet high-frequency requirements) may cause signal problems or board failure.
Mismatched coefficients of thermal expansion (CTE) of different materials may cause delamination or cracks.
Solution suggestion:Select the appropriate board according to application requirements (such as ROGERS material for high-frequency boards).
Ensure that the properties of the selected material (such as dielectric constant, coefficient of thermal expansion) match the design requirements.
9. Insufficient test pointsProblem:Insufficient test point design or unreasonable location will increase the difficulty of post-production testing.
Failure to provide sufficient electrical test points may result in failure to effectively detect faults.
Solution suggestions:Provide necessary test points for each signal in the PCB design.
Ensure that the spacing and size of the test points meet the requirements of automatic test equipment (ATE).
10. Ignoring manufacturing tolerancesProblem:Failure to consider manufacturing tolerances (such as aperture error, line width error) may cause board function failure.
Unreasonable tolerance design will increase manufacturing costs or production failure rate.
Solution suggestions:Clearly define the tolerance range of each parameter during design and ensure that it meets the manufacturer's capabilities.
Communicate with the manufacturer about its process capabilities to avoid unnecessary tight tolerances.
In order to reduce DFM issues in PCB manufacturing, the design phase should work closely with the manufacturer to understand its process capabilities and limitations and ensure that the design meets production requirements. Through reasonable design optimization, not only can production costs be reduced, but also product reliability and performance can be improved.