The impact of fingerprints on SMT patch processing
One-stop PCBA manufacturer talks about the adverse effects of fingerprints on SMT patch processing? SMT patch processing is a process of directly installing surface mount components (SMD) on the surface of electronic components. Fingerprints may have adverse effects on SMT PCB patch processing, mainly reflected in the following aspects.
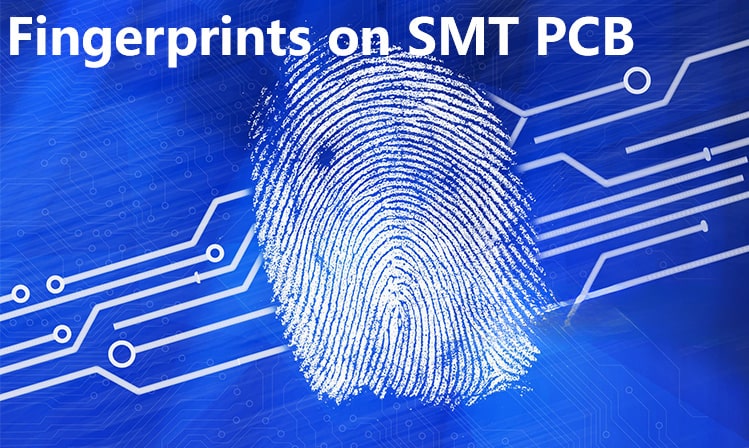
Fingerprints may have the following effects on surface mount technology (SMT) patch processing:
Contaminate the welding surface:
Grease, sweat and other contaminants on the fingerprints will contaminate the welding surface, resulting in the inability of the welding point to form a good welding connection. This will affect the quality and reliability of the solder joint.
Hinder solder wetting:
Grease and dirt in fingerprints will hinder the wetting of solder, resulting in the inability of solder to evenly cover the welding area, forming poor solder joints or empty soldering.
Increase oxidation:
The salt and moisture in the fingerprints will accelerate the oxidation process of the metal surface, making it difficult to remove the oxide layer during welding, thereby affecting the welding quality.
Impact on electrical performance:
Contaminants in fingerprints may cause degradation of electrical performance, increase resistance or form electrical leakage paths, affecting the normal operation of the circuit board.
Reduced reliability:
Due to the above problems, the mechanical strength of the solder joints and the reliability of electrical connections will decrease, which may cause product failures during use.
In order to avoid these problems, the following measures should be taken during SMT patch processing:
Keep the working environment clean: Ensure that the operator's hands are clean and try to avoid direct contact with PCBs and components.
Use anti-static gloves: Operators should wear anti-static gloves to operate to prevent static electricity from damaging components and avoid fingerprint contamination.
Clean equipment and tools regularly: Keep equipment and tools such as patch machines, steel meshes, and welding tables clean, and perform regular maintenance.
Train operators: Improve the quality awareness and operating skills of operators to ensure that each link meets the process requirements.
Through these measures, the impact of fingerprints on SMT patch processing can be effectively reduced, and the quality and reliability of products can be improved.
Then PCBAMake is the core concept we always adhere to during the PCBA manufacturing process. We are well aware that even tiny fingerprints can have a significant impact on the performance and reliability of products. Therefore, we strictly control every link to ensure the excellent quality of our products.