The difference between IPC PCB standards and how should we choose?
In the process of PCB manufacturing, there are two relatively important industry standards, IPC-6012 and IPC-A-600. These standards provide comprehensive guidance and requirements for the quality and reliability of PCBs. Professional engineers will make professional decisions based on different project requirements by understanding the difference between IPC-6012 and IPC-A-600.
Today, we will explore the importance of the two standards and the main differences between them.
IPC PCB Manufacturing Standards
IPC PCB standards refer to a series of standard specifications for PCB design, manufacturing and assembly formulated by the International Association for Printed Circuit Boards (IPC). These standards cover all aspects of PCBs, including design, materials, processes, quality control, etc., and are of great significance for ensuring the quality and reliability of PCBs. In the PCB industry, following IPC standards has become an industry consensus and an important means to improve the quality and reliability of PCBs.
The importance of IPC standards in the PCB manufacturing process
Design stage: The IPC standard specifies the layout, size, line width, line spacing and other parameters of the PCB, ensuring that the PCB has good electrical performance and solderability. In addition, the IPC standard also sets requirements for the format and content of the design file, making it easier for manufacturing and assembly personnel to understand and implement the design requirements. It also helps to produce PCBs compatible with different brands.
Process: The IPC standard specifies welding processes, assembly processes, and testing processes to ensure that PCBA can work stably and reliably. These standards help improve production efficiency, reduce production costs, and enhance market competitiveness.
Material: The IPC standard sets requirements for PCB substrates, solder, packaging materials, etc., ensuring the environmental performance and reliability of the PCB.
Quality control: The IPC standard specifies various testing methods and standards to ensure that the quality of PCBA meets the requirements.
The importance of IPC standards in the PCB manufacturing process is self-evident. Following IPC standards also helps PCBA manufacturing companies to keep pace with the international market, meet the international market's requirements for product quality and environmental performance, and expand the international market. At the same time, the continuous improvement and updating of IPC standards will help promote the improvement of the technical level of the PCBA manufacturing industry and the development and progress of the industry.
IPC standards play a vital role in promoting the continuous improvement of PCB production processes. These standards are regularly reviewed and updated to integrate the latest technological advances and industry practices. By complying with the latest IPC standards, manufacturers can stay ahead of the industry and use cutting-edge manufacturing technology to produce the best quality products.
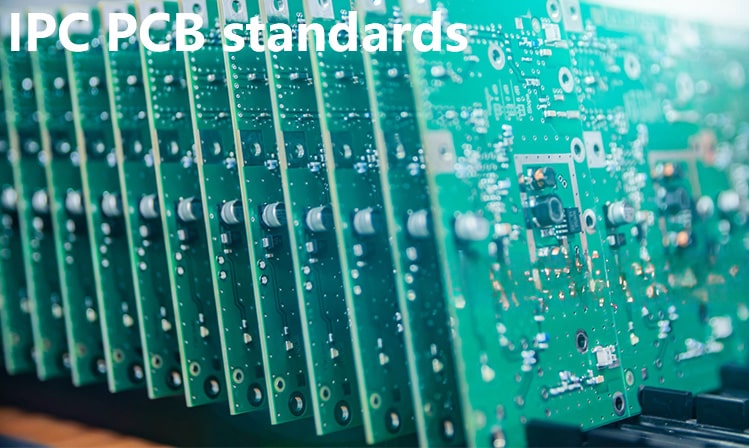
What is the difference between IPC-6012 and IPC-A-600? How should we choose?
The importance of IPC standards is already understood. Now, let's take a deep look at the main differences between IPC-6012 and IPC-A-600.
IPC-6012 and IPC-A-600 are two key PCB (printed circuit board) standards that differ significantly in their focus, usage scenarios, and content. The following are the specific differences between the two standards:
1. Different focus
IPC-6012: Performance and qualification specifications
Focus: Mainly focuses on the performance and qualification standards of rigid printed boards.
Content: Covers requirements in terms of materials, processes, design, electrical properties, mechanical properties, and environmental adaptability.
Goal: Ensure the consistency and reliability of printed boards in terms of function and performance.
IPC-A-600: Acceptability standards
Focus: Mainly focuses on the appearance quality and acceptability standards of printed boards.
Content: Describes in detail the acceptability of various appearance defects (such as surface defects, lamination defects, hole defects, etc.), and contains a large number of pictures and legends.
Goal: Ensure that the appearance quality of printed boards meets the expected standards.
2. Different use stagesIPC-6012: Manufacturing and design stage
Use stage: Mostly used in the design and manufacturing stage.
Application scenario: Formulate and evaluate the performance indicators of printed boards, and guide manufacturers to produce printed boards that meet performance requirements.
IPC-A-600: Inspection and evaluation stage
Use stage: Mostly used in the quality inspection and evaluation stage.
Application scenario: Check and evaluate the appearance quality of printed boards, determine whether there are appearance defects, and determine whether these defects are within the acceptable range.
3. Different scope of application
IPC-6012: Performance and identification
Scope of application: Applicable to the manufacture of rigid printed boards, covering different application scenarios (such as ordinary electronic products, high-performance electronic products and high-reliability electronic products).
Quality level: Provides three levels of quality standards: Class 1 (ordinary), Class 2 (high performance) and Class 3 (high reliability).
IPC-A-600: Appearance quality
Scope of application: Applicable to the appearance quality inspection of all types of printed boards, not limited to rigid printed boards.
Acceptability: The acceptability standards for different types of defects are specified in detail, and are applicable to quality assessment during the production process and the inspection stage of finished products.
4. Different specific contents
IPC-6012:
Material requirements: Specifies the selection and use requirements of printed board materials.
Process requirements: Covers the specific requirements of each process link from design to manufacturing.
Performance testing: Including test methods and requirements for electrical properties, mechanical properties and environmental adaptability.
IPC-A-600:
Defect classification: Describes in detail the types of various defects such as surface defects, lamination defects, and hole defects.
Images and legends: Provides a large number of images and legends to help identify and evaluate specific defects.
Acceptability standards: Specifies the acceptability standards for each defect at different quality levels.
Selection and use:
Use IPC-6012:
When it is necessary to develop and evaluate the performance indicators of printed boards.
In the manufacturing and design stages, it is used to guide manufacturers to produce printed boards that meet performance requirements.
Applicable to ensuring the consistency and reliability of printed boards in terms of function and performance.
Use IPC-A-600:
When a printed board appearance quality inspection is required.
During the quality inspection and evaluation stage, it is used to identify and evaluate the appearance defects of printed boards.
It is suitable for ensuring that the appearance quality of printed boards meets the expected standards.
Features
| IPC-6012
| IPC-A-600
|
Focus
| Performance and identification specifications
| Appearance quality and acceptability standards
|
Use stage
| Design and manufacturing stage
| Quality inspection and evaluation stage
|
Scope of application
| Manufacturing of rigid printed boards
| Appearance quality inspection of all types of printed boards
|
Quality level
| Class 1, Class 2, Class 3
| Acceptability standards for different types of defects
|
Contents
| Materials, processes, design, electrical properties, mechanical properties, environmental adaptability
| Acceptability standards for surface defects, lamination defects, hole defects, etc.
|