The difference between IPC 1, IPC 2, and IPC 3
Which one is more suitable for your product?Classification of IPC grades
There are currently three performance classifications used in PCB manufacturing. Each category is a grade standard established by IPC according to IPC-6011. These grades not only clarify the quality of the boards, but also their functions, performance, and inspection frequency.
IPC Class 1 Standard
IPC 1 PCBs have relatively low production and testing requirements, allowing a certain degree of defects such as larger pad voids and wire spacing errors. They are mainly used in consumer electronics such as toys, home appliances, and other low-cost, low-demand products. If your product is a cost-sensitive consumer electronic product with low performance and reliability requirements, IPC 1 is a suitable choice.
IPC Grade 2 Standard
IPC 2 grades are suitable for most electronic products. IPC Grade 2 electronic components have a longer life and higher quality than Grade 1. They cover household appliances such as microwave ovens, smartphones, laptops, TVs, air conditioners, etc. Grade 2 standard PCBs are designed to focus on continuous operation, and these devices have significant performance in function. If your product needs to work in a medium-complexity application environment and has certain reliability requirements (such as computers and communications equipment), IPC 2 is a suitable choice.
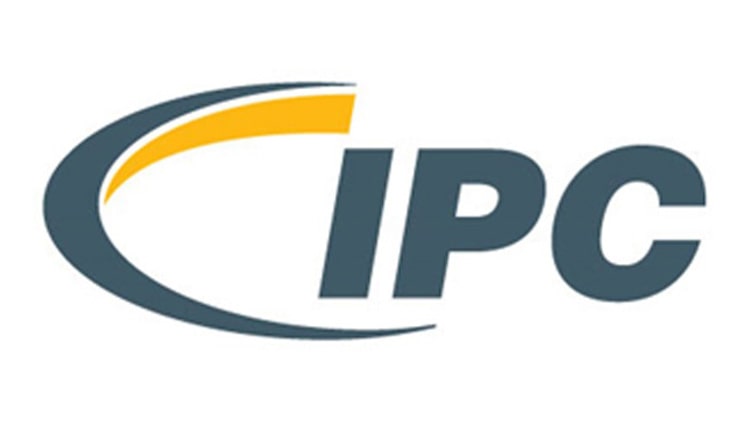
IPC Class 3 Standard
IPC Class 3 is suitable for high-performance electronic products, often used in mission-critical and high-reliability applications. The production and testing requirements are almost no defects and the requirements are the most stringent. Examples of electronic products manufactured to Class 3 standards include medical devices and equipment used in aerospace. Ensure that the product can work stably in the most demanding environments. If your product must work in extreme environments and any failure may have serious consequences (such as medical devices and avionics), IPC 3 is a must-choose level.
What does IPC Class 3 Standard mean?
IPC Class 3 Manufacturing Standard Represents IPC Class 3 Standard represents the highest quality and reliability requirements in the PCB industry, suitable for the most demanding application environments and the most stringent performance requirements. Choosing IPC Class 3 standard means the highest commitment to product quality and reliability, ensuring that the product can work stably for a long time and minimize failure rates in mission-critical and high-reliability applications.
To meet the stringent standards of Class 3 manufacturing, special equipment and processes are used to assemble these boards, and although production time and costs may increase, these are to ensure that the final product meets high standards of reliability and performance.
What grade of PCB do I need?
Does your product require Class 3 PCBs, or will Class 2 PCBs suffice? To figure out which classification is better for your product, the best way is to take a deep look at the end function of the device. While the increased performance may make the product more attractive, whether it is worth paying for a higher cost PCB needs to be carefully weighed against the actual needs of the end product.
The manufacturing quality of the Class 3 standard is undisputed, but not all devices require it. Therefore, IPC also has lower grades, and we will explain the key differences between Class 2 and Class 3 boards.
Advantages of IPC Class 2
Design: Having a Class 2 board makes the placement and routing of components much simpler, which reduces costs all around.
Manufacturing: Assembling a Class 2 board does not require as much time or materials as a Class 3. Class 2 manufacturing requirements are generally lower compared to Class 3.
Inspection: Since Class 2 PCBs are not typically used in harsh environments or facilities that require a high degree of functionality, inspection time is significantly reduced.
IPC Class 3 Advantages
Design: Class 3 PCBs must meet more stringent standards in terms of specifications and tolerances, so the extra cost pays off with longer periods of high-quality performance. By investing more time in designing these boards, you can achieve the long, trouble-free operation that users expect.
Manufacturing: The process of manufacturing Class 3 boards is much slower than that of Class 2. The process is characterized by a higher priority for installation and cleaning compared to the process of manufacturing Class 2 boards.
Inspection: Each Class 3 board undergoes rigorous inspection. Repeated inspections of IPC Class 3 PCBs help catch errors early in the manufacturing process, but this comes at the expense of production time and ultimate cost.
How to Choose the Right IPC Grade for Your Product
Choosing the right IPC grade for your product requires a comprehensive consideration of the product's application scenario, performance requirements, reliability needs, and cost factors. Ultimately, the choice of which board to use depends on the functional requirements of the product for the end user.