Reasons and functions of PCB panelization and board edge processing
As a core component in the electronic manufacturing industry, the production process of PCB involves multiple links and fine processes. In this process, panelization and board edge processing are regarded as indispensable and important steps, which can not only improve production efficiency, but also ensure the quality and aesthetics of the product.
The role of panelization and board edge processing in PCB production
The purpose and benefits of panelization
Panelization is the process of combining multiple single boards in a certain arrangement to form a larger board for production.
In PCB production, panelization has the following important functions and benefits:
1. Improve production efficiency: Through panelization, multiple single boards can complete the production process at one time, such as drilling, electroplating, etching, etc. This can not only reduce the equipment adjustment time and the number of manual operations, but also reduce the material loss in the production process, thereby significantly improving production efficiency.
2. Save material costs: Panelization can make more full use of raw materials and reduce the waste of scraps. In PCB production, many raw materials such as copper foil and substrate are purchased according to standard sizes. Through panelization, the use of boards can be more reasonably planned and material costs can be reduced.
3. Convenient for subsequent processing: The PCB after panelization can be operated in batches in the subsequent processing process, such as SMT patching, plug-in, testing, etc., to improve processing efficiency. At the same time, panelization also helps to maintain the consistency between the single boards and reduce the quality differences caused by individual processing.
4. Enhance structural stability: The PCB after panelization has better overall structural stability. In the production process, such as drilling, electroplating and other links, panelization can effectively prevent the single board from being deformed or damaged due to uneven force.
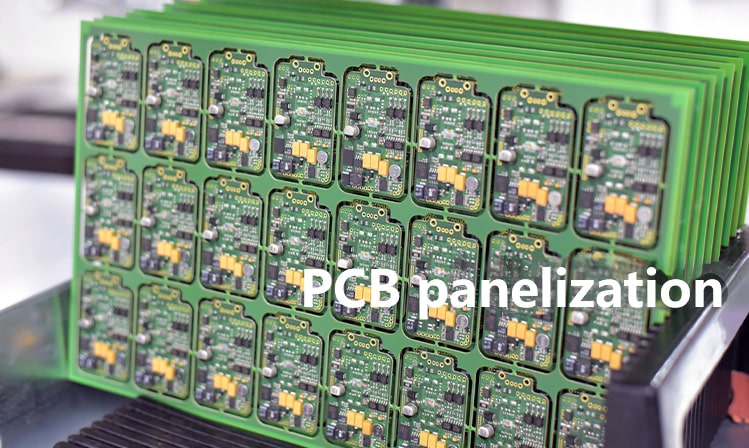
The purpose and benefits of board edge processing
Board edge processing is to process the edge of the PCB to achieve specific functions and effects. In PCB production, board edge processing also plays an important role, and its benefits are mainly reflected in the following aspects:
1. Prevent burrs and flash: In the PCB production process, especially in drilling, cutting and other links, burrs and flash are prone to occur. These burrs and flash not only affect the appearance quality of the PCB, but may also cause functional problems such as circuit short circuits. Through board edge processing, such as chamfering, deburring and other processes, these potential quality risks can be effectively eliminated.
2. Improve insulation performance: Board edge treatment can enhance the insulation performance of the PCB edge. In PCB design, important circuits and components are often distributed in the edge area. If the edge is not properly treated, it may cause leakage or breakdown between circuits. Through proper board edge treatment, such as coating insulating materials or increasing edge spacing, the insulation performance of the PCB can be improved to ensure the stable operation of the circuit.
3. Facilitate plug-in and installation: Board edge treatment can facilitate the plug-in and installation of PCBs. For example, setting positioning holes, slots and other structures on the edge of the PCB can be easily connected and fixed with external devices or components. In addition, proper board edge treatment can also improve the plug-in performance and wear resistance of the PCB.
4. Enhance aesthetics: Board edge treatment also has a positive effect on improving the overall aesthetics of the PCB. Through chamfering, polishing and other process treatments, the PCB edge can be made smoother and neater, and the visual effect and quality of the product can be improved.
Synergy between panelization and board edge treatment
In PCB production, panelization and board edge treatment are often interrelated and synergistic. Reasonable panel design can facilitate board edge processing, and vice versa.
For example, reserving appropriate spacing and positioning holes when panelizing can provide accurate positioning and processing benchmarks for subsequent board edge processing. At the same time, board edge processing can also be optimized according to the characteristics of the panel, such as uniformly processing the chamfering and deburring processes of the panel edges to improve production efficiency and product quality.
Panelization and board edge processing play a vital role in PCB production. They can not only improve production efficiency and reduce costs, but also ensure product quality and aesthetics. By deeply understanding the principles and methods of panelization and board edge processing, and optimizing and improving them in combination with actual production, new vitality can be injected into the development of the electronics manufacturing industry.