What are the factors that affect the price of blind hole PCB proofing?
With the trend of increasing miniaturization and high performance of modern electronic devices, the design and manufacturing technology of multi-layer PCB printed circuit boards are constantly improving. Among them, blind hole PCB, as a specially designed type of circuit board, plays an important role in high-end electronic products with its unique structure and manufacturing process.
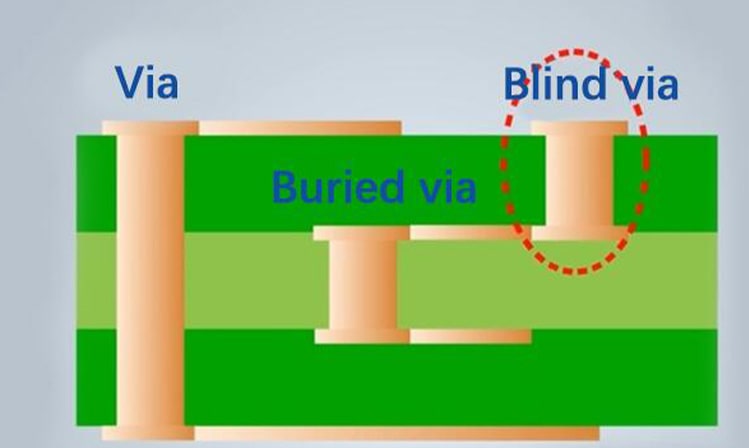
Factors affecting the price of blind hole PCB proofing
What is a blind hole PCB?
A blind hole printed circuit board (PCB) is a circuit board with a special design, whose holes are visible only on one side and covered on the other side. This design can effectively save space and increase circuit density. At the same time, it enables the circuit board to achieve higher density wiring in a limited space, which is particularly suitable for high-density interconnection (HDI) technology. Blind hole PCB is widely used in products such as smartphones, tablets, wearable devices, etc. that require extremely high space utilization.
Why is the price of blind hole PCB proofing relatively high?
1. Complex manufacturing process
Multiple processes: The processing of blind hole PCB requires a more complex process flow, including precise positioning, drilling, electroplating and other steps. For example, blind hole PCBs using laser drilling technology are usually more expensive because this technology requires higher equipment investment and technical level. These additional processes not only increase production time, but also increase manufacturing difficulty and failure rate, directly pushing up costs.
Precision requirements: The processing of blind holes requires extremely high precision and extremely small errors, so stricter process control and higher technical levels are required.
2. Special equipment and materials
High-precision equipment: The processing of blind holes often requires the use of advanced drilling equipment and high-precision laser drilling technology, as well as special electroplating processes to ensure the conductivity of the hole wall. The cost of these special equipment is much higher than that of ordinary PCB manufacturing equipment.
Advanced materials: Blind hole PCBs require the use of advanced materials to ensure their stability and reliability, and these materials are expensive.
3. Economy of scale under low production
Small batch production: The proofing stage usually involves small batch production, and in the production of blind hole PCBs, small batches mean an increase in unit cost. Since the cost of preliminary preparation (such as mold making and equipment debugging) is spread over fewer products, the price of a single blind hole PCB sample is relatively expensive. Generally speaking, the more proofs there are, the lower the production cost of a single PCB. Large-volume production can effectively dilute fixed costs, so it is recommended to increase the quantity as much as possible during proofing to reduce the unit price.
4. Quality control and inspection
Strict inspection: Inspection of blind hole PCB finished products requires advanced inspection methods, such as X-ray inspection, to ensure the quality and reliability of the holes. These inspection equipment and processes also increase costs.
Price range of blind hole PCB proofing
The specific price varies depending on many factors (such as the number of board layers, the number and diameter of holes, material selection, surface treatment, etc.). The price of basic blind hole PCB proofing may start from a few hundred yuan, and as the complexity of the design increases, the price can easily reach thousands or even tens of thousands of yuan. The following are several key factors that affect the price:
1. Number of board layers: The more layers, the more complex the manufacturing process and the higher the cost.
2. Number and diameter of holes: The number and diameter of holes directly affect the difficulty and cost of drilling.
3. Material selection: The cost of high-performance materials (such as high-frequency materials and high-temperature resistant materials) is significantly higher than that of ordinary materials.
4. Surface treatment: Different surface treatment methods (such as electroplating, immersion gold, tin spraying, etc.) have different costs.
5. Design complexity: The more complex the design, the more difficult it is to process, and the cost increases accordingly.
When making PCB samples, customers should consider these factors comprehensively according to their own needs and budget to obtain the best cost-effectiveness. Through reasonable planning and selection, you can control costs while ensuring quality, providing strong support for the development of electronic products.