How to ensure that BGA boards are fast and good in SMT processing
BGA (Ball Grid Array) packaging is widely used in modern electronic products due to its high density and good electrical performance. However, the soldering process of BGA is relatively complicated. How to ensure that it is completed quickly and with high quality in SMT (Surface Mount Technology) processing is a concern for many manufacturers. We can improve from the following key factors.
Design Optimization
Reasonable Layout
During the PCB design stage, ensure that there is enough space around the BGA components. This can reduce the interference of adjacent components and facilitate rework and inspection. In addition, a reasonable layout helps to evenly distribute heat and reduce thermal stress.
Pad Design
Depending on the size and spacing of BGA, the design of the pad is crucial. The correct pad size and shape can effectively improve the quality of soldering and reduce the risk of bridging and voids.
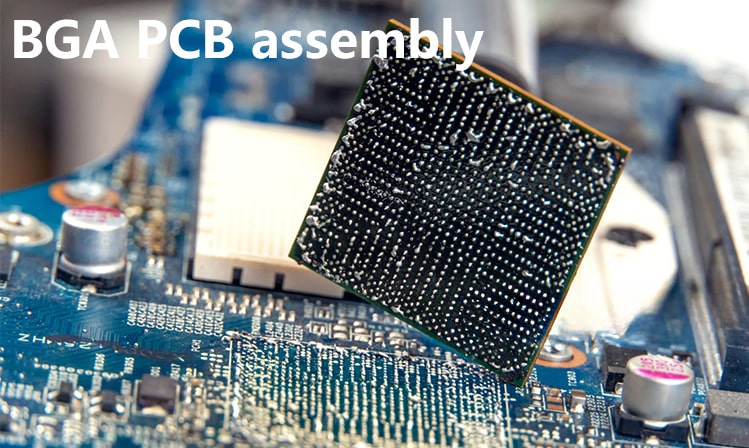
Material Selection
High-quality Solder Paste
It is very important to choose a solder paste suitable for BGA. Consider its viscosity, melting point and wettability. High-quality solder paste can improve the reliability of solder joints and reduce defects.
Substrate Material
Using the right substrate material can reduce warping and thermal expansion. Selecting materials with thermal expansion coefficients that match BGA can help improve soldering quality.
Equipment calibration
Precision placement machine
The precision and stability of the placement machine directly affect the placement quality of BGA. Ensure that the equipment is calibrated and maintained regularly to avoid offset and misalignment.
Reflow oven temperature curve
Optimize the temperature curve of the reflow oven according to the characteristics of BGA and solder paste. Appropriate heating and cooling rates can avoid soldering defects.
Process control
Printing process
Ensure uniform printing of solder paste. Using appropriate template thickness and opening design can reduce the occurrence of bridging or defects.
Placement process
Use high-precision equipment to ensure accurate BGA alignment. Vibration and shock should be avoided during placement to prevent displacement.
Quality inspection
X-Ray inspection
X-Ray can check the internal structure of the solder joint and identify potential problems such as voids and short circuits. Regular X-Ray inspection helps to detect problems early.
AOI (Automated Optical Inspection)
AOI is used to check the appearance and soldering quality. By detecting the shape and size of the solder joint, ensure that the soldering meets the standards.
Training and Management
Personnel training
Ensure that operators are proficient in equipment operation and process flow, update training content in a timely manner, and improve their skills.
Strict management
Establish standardized operating procedures and quality management systems to ensure that each link meets regulatory requirements.
Through the above measures, PCBA manufacturers can effectively improve the efficiency and quality of BGA boards in SMT processing. This can not only reduce production costs, but also improve the market competitiveness and reliability of products.