Which is better, SMT or DIP in PCBA processing of circuit boards?
The difference between SMT and DIP in PCBA processing
In the electronics manufacturing industry, SMT (surface mount technology) and DIP (dual in-line package) are two common ways to install electronic components. For purchasing personnel of electronic product companies, when choosing SMT or DIP, they need to consider many factors, including production cost, production efficiency, product quality, maintainability, and market trends. So, which is better for circuit board processing SMT and DIP?

The difference between SMT and DIP in PCBA processing
1. Production cost comparison
Production cost is one of the important factors that electronic product companies need to consider when choosing SMT or DIP. Generally speaking, the production cost of SMT is relatively low. This is because SMT uses an automated production line to mount components, which greatly improves production efficiency and reduces labor costs. In addition, the components used by SMT are small in size, which can save circuit board space, thereby reducing the use of raw materials.
In contrast, the production cost of DIP is relatively high. The insertion process of DIP components usually needs to be completed manually, which not only reduces production efficiency but also increases labor costs. At the same time, DIP components are larger in size and occupy more circuit board space, resulting in higher raw material costs.
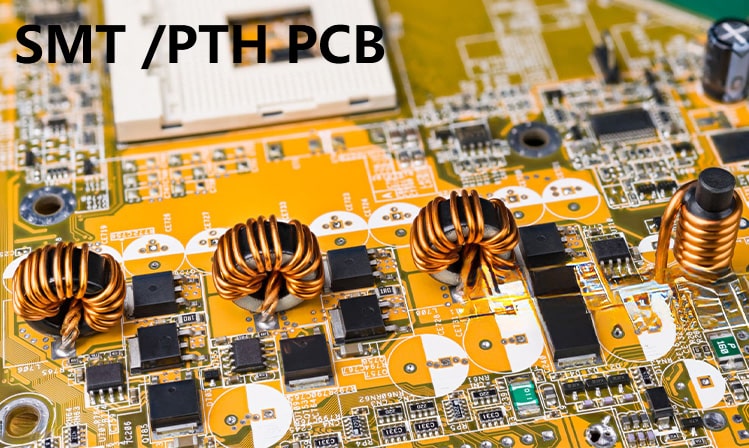
2. Comparison of production efficiency
In terms of production efficiency, SMT has obvious advantages. Since SMT uses an automated production line, it can achieve high-speed and precise component placement, greatly improving production efficiency. In addition, the flexibility of the SMT production line is also very high, and the production rhythm and production capacity can be easily adjusted to meet the needs of different customers.
However, the production efficiency of DIP is relatively low. Since the insertion process of DIP components needs to be completed manually, the production speed is greatly limited. At the same time, the flexibility of the DIP production line is poor, and it is difficult to quickly adjust the production rhythm and production capacity.
3. Comparison of product quality
In terms of product quality, SMT and DIP have their own advantages and disadvantages. SMT uses an automated production line to achieve high-precision component placement, thereby ensuring the stability and reliability of the product. In addition, the small size and light weight of SMT components make the product lighter and more beautiful.
Although DIP may have certain human errors in the manual insertion process, it has advantages in certain specific application scenarios. For example, in applications that need to withstand greater mechanical stress or high temperature environments, the pins of DIP components can provide better mechanical support and heat dissipation.
4. Maintainability Comparison
In terms of maintainability, DIP is relatively more advantageous. Because the pins of DIP components are long and easy to operate, it is more convenient and quick to repair and replace components. In addition, the identification of DIP components is clear and easy for engineers to troubleshoot and repair.
In contrast, the repair and replacement of SMT components is relatively difficult. Due to the small size and short pins of SMT components, higher precision and skills are required for repair. At the same time, the identification of SMT components is usually vague, which brings certain difficulties to troubleshooting.
5. Market Trend Analysis
With the continuous development of electronic technology, SMT has become the mainstream technology in the electronic manufacturing industry. More and more electronic product companies choose to use SMT for production to improve production efficiency, reduce costs and meet the market demand for thin and miniaturized products.
However, DIP still has certain demand in certain specific fields and markets. For example, in some military, aerospace and other fields with extremely high reliability requirements, DIP is widely used due to its good mechanical support and heat dissipation effect.
SMT and DIP have their own advantages and disadvantages. The choice of which technology depends on the specific application scenario and needs. In most cases, SMT is the first choice due to its advantages in production cost, production efficiency and meeting market demand. But in some specific fields and scenarios, DIP still has irreplaceable value.
Which is better, SMT or DIP in PCBA processing of circuit boards? Knowledge points about the difference between SMT and DIP in PCBA processing. If you want to know more, you can pay attention to PCBAMake. If you need to know more about PCB proofing, SMT patch, and PCBA processing related technical knowledge, please leave a message to get it!
www.pcbamake.com