The role of SPI and its impact on quality
The first step of the SMT process is solder paste printing, which is also the first quality control checkpoint in the PCBA production process, SPI solder paste inspection.
What is SPI?
First of all, SPI refers to solder paste inspection equipment in the PCBA processing industry, and solder paste inspection--Solder Paste Inspection is therefore referred to as SPI. SPI and AOI have similarities. Both PCBA inspection equipment use optical images to check quality, but SPI checks the printing volume, flatness, height, volume, area, height deviation (pull tip,) offset, defects and damage of solder paste after solder paste printing.
In the production process of SMT patches, we found that the amount of printed solder paste is related to the reliability and quality of the joints: too much or too little will turn into unreliable joints, which has a great impact on product quality and is unacceptable. And according to industry statistics, in all SMT assembly processes, up to 75% of defects are caused by poor solder paste printing, so the quality of solder paste printing process largely solves the quality of SMT process.
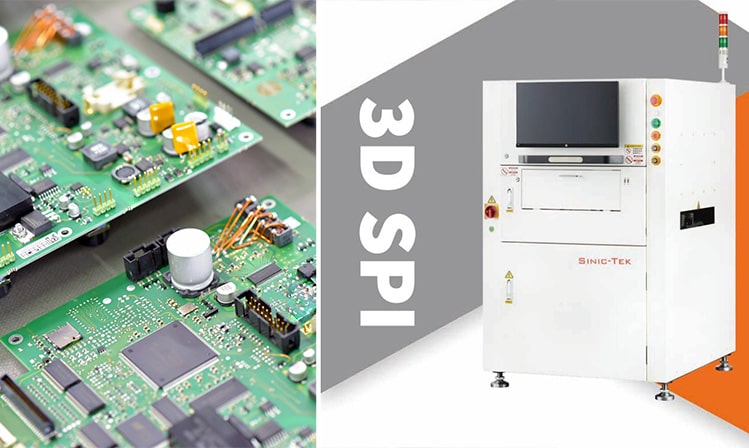
What are the advantages of SPI?
1. Reduce defects
Solder paste printing is the first step of the entire patch assembly, and SPI is the first step of quality control in the PCBA manufacturing process. The birth of SPI solder paste detection equipment aims to closely monitor the printing of solder paste during solder paste printing. In this link, the machine is used to detect poor solder paste printing, such as insufficient solder paste, excessive solder paste, bridging, etc. It can intercept poor solder paste at the source and effectively avoid the defective products caused by the flow of such PCB boards to the next process for continued production.
2. Improve efficiency
The defective boards checked after reflow soldering need to go through planning, material removal, board washing and other processes. At the same time, SMT processing has a lot of 0201 and 01005 materials, which is undoubtedly a long rework for manufacturers. The repair time of the defective boards detected by SPI is much shorter and easy to rework. They can be reworked immediately and put back into production, saving a lot of time and improving production efficiency.
3. Save costs
In the early stage of SMT assembly, if the SPI machine is used to detect defects, the rework can be completed in time, which saves time and cost. On the other hand, it can save production costs by avoiding the delay of defective boards to the later manufacturing stage, which will cause poor functionality of PCBA boards.
4. Improve reliability
As we said before. In SMT patch processing, 75% of defects are caused by poor solder paste printing, and SPI can accurately intercept poor solder paste printing in the SMT process and strictly control the source of defects, which is conducive to reducing defects and improving product reliability.
Nowadays, products are becoming more and more miniaturized, and components are constantly changing, while improving performance and reducing volume. For example, 01005, BGA, CCGA, etc. have higher requirements for solder paste printing quality. Therefore, in the SMT process, SPI has become an indispensable quality control process. Every professional and dedicated PCBA factory should be equipped with SPI solder paste detection equipment in SMT assembly.
PCBAMake factory is equipped with professional SPI equipment to protect your products. If you have pcb, pcb assembly, component procurement, shell packaging, etc., you can contact us at any time.