Effective methods to solve the problem of uneven FPC patch processing
In the field of electronic manufacturing, FPC patch processing is a crucial link. However, in the actual production process, the problem of uneven FPC patch processing often troubles production personnel. This problem not only affects the appearance quality of the product, but also may lead to serious consequences such as poor electrical connection and unstable performance. Therefore, solving the problem of uneven FPC patch processing is of great significance to improving product quality and production efficiency.
Effective methods to solve the problem of uneven FPC patch processing
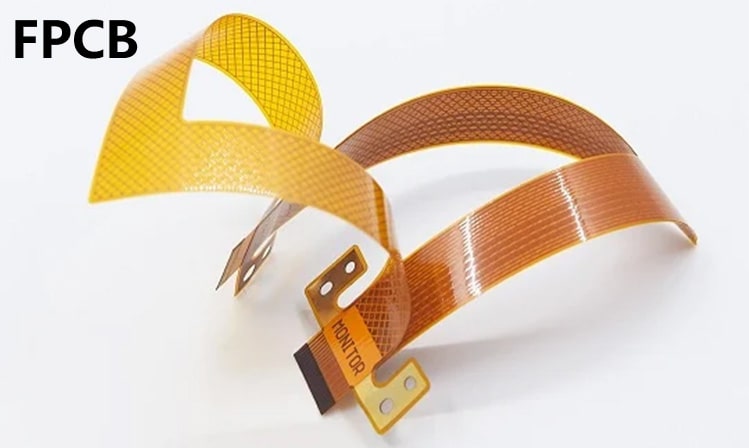
Cause analysis:
1. Material factors: Uneven quality or warping of FPC substrate, uneven coating or incomplete curing of glue may lead to uneven patch processing.
2. Equipment factors: The accuracy and stability of the patch machine have a decisive influence on the quality of patch processing. Inaccurate positioning, uneven conveyor belt or severe wear of the nozzle may cause positional displacement or unevenness of FPC during processing.
3. Improper process parameter settings: Unreasonable process parameters such as temperature, pressure, and time may cause FPC to be uneven. For example, excessive temperature may cause deformation of the FPC substrate, and excessive pressure may cause the components to be crushed or displaced.
4. Operational factors: The operator's proficiency and sense of responsibility also have an important impact on the quality of patch processing. Unskilled operation or carelessness may cause the unevenness of the FPC.
Solution:
1. Select high-quality materials: Select FPC substrates with stable quality and uniform thickness, and ensure that the glue is evenly applied and fully cured.
2. Improve equipment performance: Regularly maintain and service the patch machine to ensure equipment accuracy and stability. Adjust and repair problems such as inaccurate positioning and uneven conveyor belts in a timely manner.
3. Optimize process parameters: According to the characteristics of the FPC substrate and the requirements of components, reasonably set the process parameters such as temperature, pressure and time during the patch processing. Find the best combination of process parameters through experiments.
4. Improve the quality of operators: Strengthen the training and management of operators to ensure that they can master the equipment operation skills and operate strictly in accordance with the process requirements.
5. Use auxiliary tools and technologies: Use fixtures or jigs to fix and support FPC, and use visual inspection systems to monitor and adjust the patch position in real time.
Example analysis:
An electronic manufacturing company encountered serious unevenness problems during the FPC patch processing. After analysis, it was found that the main reasons were unstable material quality, insufficient equipment accuracy, and improper process parameter settings. In response to these problems, the company took the above-mentioned improvement measures. After implementation, the unevenness problem of FPC patch processing has been effectively solved, product quality has been significantly improved, and customer satisfaction has also been greatly improved.
Eliminating the unevenness problem of FPC patch processing requires comprehensive consideration of multiple factors such as materials, equipment, processes and operations. Only by selecting high-quality materials, improving equipment performance, optimizing process parameters, improving the quality of operators, and using auxiliary tools and technologies can this problem be effectively solved and product quality and production efficiency can be improved.