What are the functions of the solder mask layer of PCB circuit boards?
In the field of electronic manufacturing and PCBA patch processing, the solder mask layer is an indispensable component, which plays a key role in protecting circuit boards and ensuring the reliability of electronic equipment.
The role of the solder mask layer of PCB circuit boards
1. Definition of solder mask layer
Solder mask layer, also known as solder mask or solder mask ink, is a special coating applied to the surface of printed circuit boards (PCBs). It is usually mixed with polymer resins, pigments, fillers and other additives, and is evenly coated on the copper foil surface of the PCB through processes such as screen printing, spraying or photo painting to form a thin film with insulating properties.
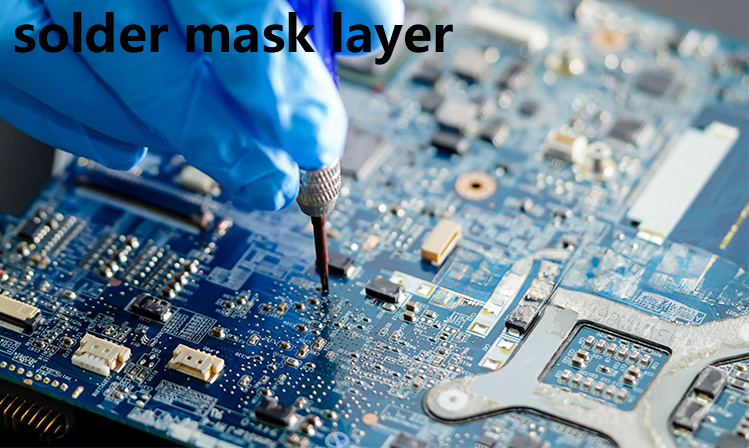
2. The role of solder mask layer
Electrical insulation: One of the main functions of the solder mask layer is to provide electrical insulation to prevent short circuits between different circuits. It can cover areas where conductivity is not required, define the boundaries of conductive paths and electrical connections, and ensure that current flows as designed.
Protect circuits: The solder mask layer can protect the circuits on the circuit board from environmental factors such as dust, moisture, chemicals and physical damage. This protection is essential to ensure the long-term reliability and stability of the circuit board.
Enhanced aesthetics: Solder masks are usually colored, which not only improves the appearance of the circuit board, but also helps with visual inspection during manufacturing and repair. Solder masks of different colors can be used to distinguish different functional areas or identify special components.
Identify components: The marks and symbols on the solder mask can be used to identify the position, direction and polarity of components, which is very helpful for the assembly and repair of circuit boards, improving the accuracy and efficiency of operations.
Heat dissipation management: Special types of solder masks have excellent thermal conductivity, which can help dissipate the heat generated by electronic components, improve the thermal stability of circuit boards, and extend the service life of electronic equipment.
3. Types of solder masks
Depending on the composition, application process and performance characteristics, solder masks can be divided into many types, including liquid photoimageable solder masks, dry film solder masks, water-based solder masks, high-temperature solder masks and flexible solder masks. Different types of solder masks have their own unique advantages and applicability in different application scenarios.
The solder mask plays a vital role in circuit board manufacturing. It not only provides electrical insulation and circuit protection, but also makes important contributions to the reliability and performance of electronic devices by enhancing aesthetics, identifying components, and managing heat dissipation.
Therefore, in the PCBA patch processing process, it is very important to reasonably select and apply the appropriate type of solder mask. For specific application requirements, choosing the right type of solder mask can maximize its role and improve the quality and performance of the circuit board.