What is the difference between reflow soldering and wave soldering in PCBA processing
In the process of printed circuit board assembly (PCBA), soldering is a crucial step, which determines whether the connection between components and circuit boards is reliable. Reflow soldering and wave soldering are the two most commonly used soldering technologies in PCBA processing, and they have significant differences in process flow, scope of application and operating principles.
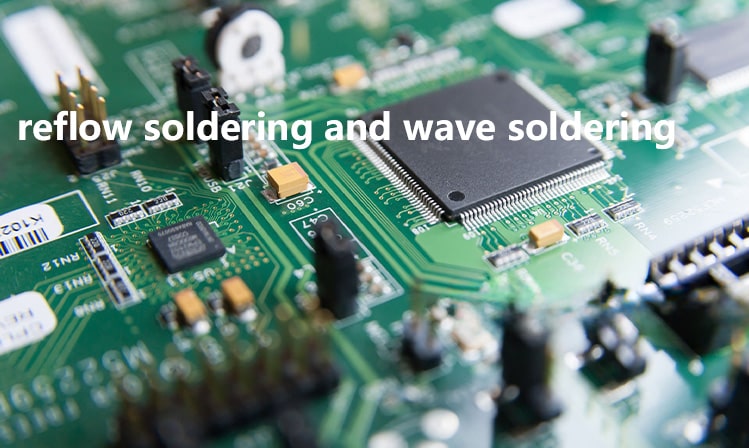
Difference between reflow soldering and wave soldering in PCBA processing
Overview of reflow soldering
1. Working principle
Reflow soldering is a soldering method that melts solder paste by heating to form a firm connection between components and PCB pads. After the surface mount components (SMD) are precisely placed on the PCB coated with solder paste, the circuit board enters the reflow soldering furnace, and after four stages of preheating, constant temperature, reflow and cooling, the soldering is finally completed.
2. Scope of application
Reflow soldering is mainly used in surface mount technology (SMT) process, and is suitable for soldering various surface mount components, such as resistors, capacitors, IC chips, etc. It is widely used in the manufacturing process of electronic products such as mobile phones, computers, and communication equipment.
3. Process flow
Solder paste printing: Precisely print the solder paste onto the PCB pad.
Component placement: Place the components onto the pad using a placement machine.
Reflow soldering: The PCB passes through a reflow oven and completes soldering at a controlled temperature.
Cooling and solidification: The solder joint cools and solidifies to form a reliable electrical connection.
Overview of wave soldering
1. Working principle
Wave soldering is a soldering method that forms solder joints between component pins and circuit board pads by immersing the PCB in a wave of molten solder. During the wave soldering process, the molten solder forms a wave crest through the nozzle, the PCB passes over the wave crest, and the solder contacts the pad and component pin to form a solder joint.
2. Scope of application
Wave soldering is mainly used in the through-hole insertion technology (THT) process, and is suitable for soldering plug-in components (DIP) such as inductors, transformers, connectors, etc. It is often used in products such as home appliances, automotive electronics, and industrial control equipment that require a large number of through-hole components to be soldered.
3. Process flow
Flux spraying: spray flux on the PCB welding surface to improve the welding effect.
Preheating: PCB enters the preheating zone and increases the temperature to reduce welding stress.
Wave soldering: PCB passes through the solder wave to complete the welding of all solder joints.
Cooling: The solder joints are cooled and solidified to ensure the welding quality.
The main differences between reflow soldering and wave soldering
1. Welding objects
Reflow soldering: Mainly used for the welding of SMT patch components, suitable for welding surface mount components, and can handle smaller and more complex components.
Wave soldering: Mainly used for the welding of THT plug-in components, suitable for welding through-hole components with pins.
2. Welding process
Reflow soldering: The solder paste is heated by controlled temperature to melt it and form solder joints. The welding process is more precise and suitable for double-sided boards and complex circuit boards.
Wave soldering: The wave crest of molten solder contacts the PCB to form solder joints. The soldering speed is fast and it is suitable for mass production but not suitable for processing small SMD components.
3. Equipment and cost
Reflow soldering: The equipment is complex and the cost is high. It is suitable for the production of precision electronic products. The reflow oven requires multi-zone temperature control to ensure the soldering quality of different components.
Wave soldering: The equipment is relatively simple and the cost is low. It is suitable for mass production of products with plug-in components, but for double-sided boards and PCBs with dense component layout, the applicability of wave soldering is low.
4. Soldering effect
Reflow soldering: The soldering effect is fine and the reliability of solder joints is high. It is suitable for high-density and high-precision PCB manufacturing.
Wave soldering: The soldering efficiency is high and it is suitable for processing a large number of identical solder joints, but the soldering accuracy is low and it is not suitable for complex and tiny components.
How to choose the right soldering process
The choice of reflow soldering or wave soldering depends mainly on the design of the PCB and the type of components used. For circuit boards dominated by SMD components, reflow soldering is the first choice. For circuit boards with a large number of through-hole components, wave soldering is more suitable. In some mixed assemblies, the two may be used in combination, with reflow soldering first and then wave soldering to complete the soldering of through-hole components.
You can follow PCBAMake. If you need to know more about PCB proofing, SMT patch, and PCBA processing related technical knowledge, please leave a message to get it!