- Home
- About us
- Products
- PCB Fabrication
- PCB Assembly&OEM
- Quality
- Blogs
- Contact
One-Stop Turnkey PCB Assembly Manufacturer
One-Stop Turnkey PCB Assembly Manufacturer
One-Stop Turnkey PCB Assembly Manufacturer
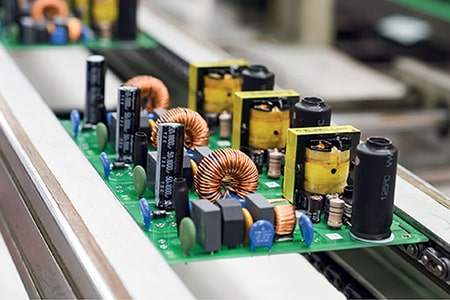