What are the factors that affect the selection of PCBA board colors
The impact of PCBA board color on PCBA processing costs
PCBA color is an optional option in PCB board design and usually does not affect the performance of the circuit board. But some people are curious whether the color selection of PCBA boards will affect its production cost.
Today we will take you to understand the factors that affect the selection of PCB board colors and the impact of different colors on the cost of processing PCBs
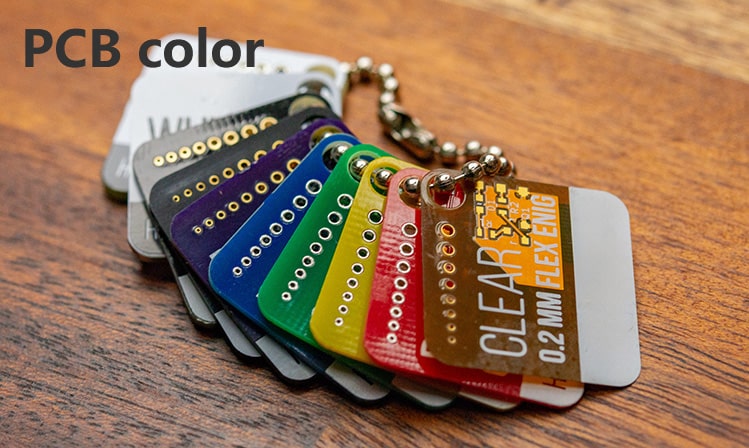
1. PCBA board color selection
The color of the PCBA board refers to the color of the solder mask layer on the surface of the PCB board. This coating can protect the copper traces on the board and prevent short circuits when soldering components. The most common color is green, because the green solder mask visually helps the factory detect defects on the circuit board and is also convenient for viewing traces and solder joints during inspection.
In addition to green, PCBA boards can also choose other colors such as red, blue, black, white and even yellow. The choice of these colors is mainly related to visual effects, brand requirements and special applications.
2. Factors affecting the selection of PCBA board colors
Functional requirements
Green is often chosen not only because it is easy to detect welding quality, but also because of its mature manufacturing process and stable formula. Other colors are not significantly different from green in terms of function, but different colors may be selected in some applications to meet specific functional requirements. For example, black PCBs are widely used in some high-end consumer electronic products to reflect their unique appearance design.
Aesthetic needs and brand image
Many technology companies choose different PCB colors based on brand image or product appearance design requirements. For example, black PCBs are generally considered to be more high-end, while red or blue are often used in customized products to make the products more unique in appearance. Such aesthetic needs usually do not affect the function of the PCB, but they will affect the user's visual perception of the product.
Manufacturability
The manufacturing process of PCBs of different colors is roughly the same, but because the solder mask of some colors (such as black or white) is not as ideal as green in terms of contrast and defect detection, this may bring additional challenges to inspection and quality control during the production process. Generally, PCBs with green solder mask make it easier for manufacturing workers to identify circuit problems, thereby improving production efficiency.
3. Potential impact of different color PCBs on production costs
Green PCBs are less expensive
The formula of green solder mask materials has been highly standardized, the manufacturing process is mature, and many equipment and inspection systems are optimized specifically for green PCBs. Therefore, green PCBs tend to be less expensive to produce and can be produced faster, reducing the chance of errors.
Other colors may increase costs
For non-standard colors such as red, blue, black or white, although the material cost difference is not large, some colors (such as black) are more difficult to detect and may require additional processes or inspection equipment. This may complicate the manufacturing process and slightly increase costs. For example, black PCBs may encounter reflection problems during inspection, making it difficult for automatic optical inspection (AOI) systems to identify solder joint defects, increasing the need and time for manual inspection.
In addition, there are relatively few suppliers of solder mask materials in non-standard colors, especially in large-scale production, where supply chain options are more limited, so the cost may be slightly higher.
Actual cases or data support
In actual manufacturing, some factories have indeed found that the production defect rate of black and white PCBs is higher and the inspection difficulty is increased, resulting in an increase in production costs. However, this cost difference is usually small, usually not more than 5% of the total cost. For most projects, such a cost difference may not significantly affect the overall budget.
Does color selection have a significant impact on cost?
The color selection of PCBA boards has a certain impact on its cost, but it is not a decisive factor. Green PCB has the lowest cost due to its mature process and widely used equipment. Other colors such as red, blue or black may increase manufacturing difficulty in specific applications, thereby slightly increasing costs.
If only from the perspective of production cost, green is usually the most economical choice; and if brand image and visual effects are critical to product design, then the increased cost can be regarded as a reasonable investment to enhance the product's appearance and market value. In most cases, the cost difference of different colors does not have a significant impact on the overall PCBA project budget, so companies can find a balance between color and cost according to their own needs.