Importance and precautions of DFM in the PCB industry
DFM mainly performs a series of checks and optimizations on the design of the circuit board to ensure that the design can be smoothly produced by the existing PCB manufacturing and assembly processes, and reduce potential problems in production.
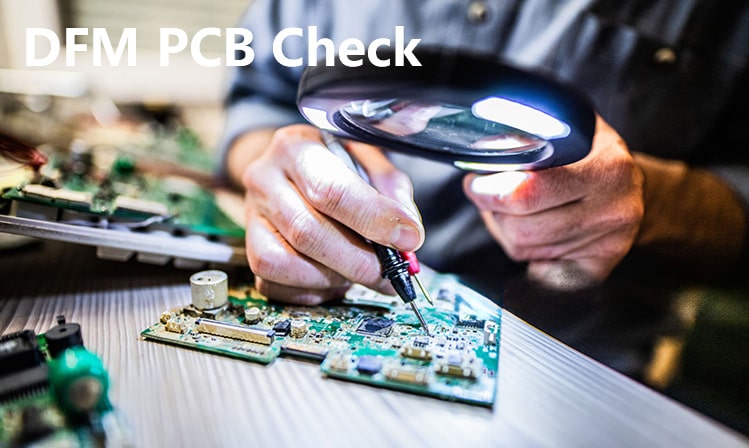
Importance of DFM inspection
1. Reduce production problems and improve yield
In PCB production, unreasonable design may lead to problems in production, such as poor welding, short circuit, open circuit, drilling offset, etc. Through DFM inspection, these problems can be found and optimized in the design stage to avoid a large number of scrap or rework in later manufacturing.
2. Shorten the product development cycle
If the design problem is found in the manufacturing stage, modification and re-production will greatly extend the product development cycle. DFM inspection can help find problems in advance in the design stage, reduce the number of modifications in the subsequent process, and thus speed up the product to market.
3. Reduce manufacturing costs
Design problems may lead to production line adjustments, additional manual intervention or high scrap rates, which will increase manufacturing costs. Ensuring that the design meets production requirements through DFM inspection can significantly reduce cost expenditures.
4. Ensure the connection between design and manufacturing
PCB design and manufacturing are two different links. Designers are often not familiar with the specific limitations of the production process, while production personnel may not understand the design intent. DFM inspection can serve as a bridge to ensure that the design can be smoothly implemented by the manufacturing process and avoid problems caused by poor communication.
What to pay attention to in DFM inspection
1. Understand the manufacturing process capabilitiesIn design, it is necessary to understand the manufacturer's process capabilities. For example:
Minimum line width and line spacing;
Minimum via size;
Stacking structure (stacking design requirements for multilayer boards);
Surface treatment methods (such as immersion gold, tin spraying, etc.).
Different manufacturers have different process limits, so you should communicate with the manufacturer to understand their capabilities before designing.
2. Comply with design rules
PCB design software usually provides DRC (Design Rule Check) function, but DFM inspection goes a step further and needs to pay special attention to the following rules:
Pad design: whether the ratio of pad to aperture is reasonable to avoid poor welding;
Spacing requirements: whether the copper foil spacing, via spacing, etc. meet the process requirements;
Wiring layout: whether the signal line is too dense, whether there are sharp corners, sharp turns and other design problems.
3. Pay attention to thermal design and heat dissipation optimization
PCB will generate heat in actual use, especially high-power circuits. DFM inspection should focus on heat dissipation design, such as whether thermal vias are added, whether the copper foil area is sufficient, whether heat dissipation materials are used, etc.
4. Inspection of vias and welding process
Via design: Check whether the via position is reasonable to avoid vias being too close to pads, resulting in short circuit problems;
Welding surface optimization: whether the pads of SMD components are reasonably designed to avoid cold soldering or bridging during welding. 5. Signal integrity and electromagnetic compatibility
Signal integrity: Is the routing of high-frequency signals short and straight enough, and does it avoid unnecessary corners and loops?
Electromagnetic compatibility (EMC): Is there a sufficient grounding layer designed, is a shielding structure added, etc.
6. Is the material selection appropriate?
Material selection has a direct impact on the performance and production of PCBs. When designing, you need to consider:
The coefficient of thermal expansion (CTE) of the material, whether it matches the components;
Whether the appropriate flame retardant grade (such as FR-4) is selected;
Whether low-loss materials are required for high-frequency applications.
7. Accuracy of file output
After completing the DFM check, when outputting files for production (such as Gerber files, drilling files, etc.), you need to ensure that the format is correct and the data is complete to avoid production problems caused by file errors.
The role of DFM in the PCB manufacturing industry cannot be ignored. It is not only a bridge between design and manufacturing, but also a core link to ensure product quality, shorten development cycles, and reduce production costs. PCBAMake provides free DFM checks. If you have pcb or pcba projects, please feel free to contact us.