Methods to avoid board bending and warping during reflow soldering
I believe everyone knows that when doing SMT patch processing, the circuit board must be reflowed after the components are mounted on the patch machine. However, board bending and board warping are prone to occur when the circuit board undergoes reflow soldering. So how to prevent board bending and board warping when the circuit board passes through the reflow oven? Today I will share with you the countermeasures.
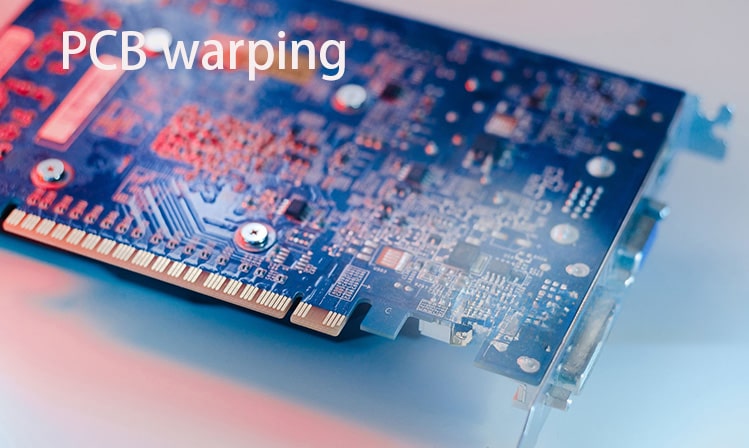
Optimize the reflow soldering process: adjust the temperature curve of the reflow soldering oven to avoid excessively high peak temperatures and excessively fast heating and cooling rates to reduce circuit board deformation due to thermal stress. At the same time, ensure that the conveyor belt speed of the reflow oven is stable to avoid uneven heating and cooling of the circuit board in the oven.
Choose the right plate: Choose a plate with a high Tg (glass transition temperature). This kind of plate has better dimensional stability at high temperatures and can resist deformation caused by thermal stress.
Increase the thickness of the circuit board: Without affecting the overall performance of the product, appropriately increasing the thickness of the circuit board can improve its ability to resist bending and warping.
Optimize circuit board design: When designing circuit boards, try to reduce the number of panels and reduce the overall size to reduce sagging deformation caused by self-weight. At the same time, arrange the components reasonably to avoid placing heavy components on one side of the circuit board.
Use auxiliary tools: During the reflow soldering process, you can use an oven tray or oven tray clamp to fix the circuit board to prevent it from moving or deforming in the furnace.
Strictly control the welding quality: ensure the uniformity and consistency of the solder during the welding process, avoid solder short circuits and other problems, thereby reducing circuit board deformation caused by poor welding.
Control preheating temperature and time: In the reflow soldering process, the preheating stage is very critical. If the preheating temperature is too high or the time is too long, it may cause thermal stress on the circuit board, which may lead to board bending or warping. Therefore, it is necessary to set the preheating temperature and time reasonably according to the material and thickness of the circuit board to ensure that the circuit board can be heated evenly and reduce the generation of thermal stress.
Use anti-deformation fixtures: During the reflow soldering process, special anti-deformation fixtures can be used to fix the circuit board. These clamps effectively support the circuit board and prevent it from deforming at high temperatures. When selecting a clamp, you need to ensure that its material is resistant to high temperatures, does not deform, and has good contact with the circuit board surface to avoid additional stress.
Optimize welding parameters: Reflow soldering parameter settings also have a great impact on the deformation of the circuit board. It is necessary to adjust parameters such as welding temperature, welding time and welding speed according to the actual situation of the circuit board to obtain the best welding effect and reduce the deformation of the circuit board.
Conduct thermal stress analysis: During the circuit board design process, finite element analysis and other methods can be used to conduct thermal stress analysis on the circuit board. By simulating the heating conditions of the circuit board during the reflow soldering process, possible deformation can be predicted, so that preventive measures can be taken in advance to reduce deformation problems in actual production.
Strengthen quality monitoring: During the production process, it is necessary to strengthen quality monitoring and regularly check the operating status of the reflow soldering equipment and the welding quality. Once a circuit board deformation problem is discovered, production should be stopped immediately, the cause of the problem should be analyzed, and corresponding measures should be taken to improve it.