The difference between lead-free solder paste and lead solder paste
Solder paste is an indispensable material in the electronics manufacturing industry, mainly used to solder electronic components to circuit boards. According to its composition, solder paste can be divided into lead solder paste and lead-free solder paste. The use of lead-free solder paste and lead solder paste is generally determined by the characteristics and application scenarios of customer products. From an environmental perspective, PCBAMake advocates that customers use lead-free solder paste as much as possible, but we also respect the choices of some customers, so what is the difference between them?
1: Composition difference
Lead solder paste
Lead solder paste is usually composed of tin (Sn) and lead (Pb), with a typical alloy ratio of 63% tin and 37% lead (Sn63/Pb37). This alloy has excellent welding performance and a low melting point (about 183°C), making it very popular in the electronics manufacturing process.
Lead-free solder paste
Lead-free solder paste does not contain lead. Common lead-free alloys include tin-silver-copper (SAC) alloys, such as SAC305 (96.5% tin, 3% silver, 0.5% copper). The melting point of lead-free solder paste is usually higher, about 217°C to 227°C.
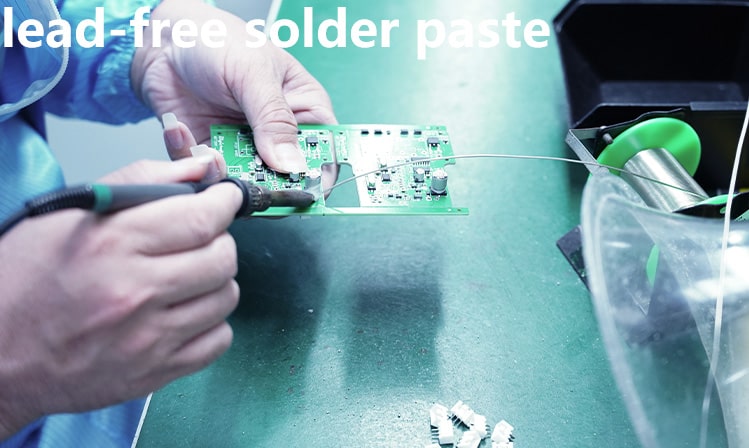
2: The difference between environmental protection and health
Lead solder paste
Lead is a toxic metal. Long-term exposure to lead can have serious effects on human health, such as damage to the nervous system, kidneys, and reproductive system. During the welding process, lead-containing fumes and dust can also cause air pollution and pose a threat to the health of operators.
Lead-free solder paste
Lead-free solder paste meets the requirements of the EU RoHS (Restriction of Hazardous Substances) directive, reducing the use of hazardous substances, thereby reducing the impact on the environment and human health. Although lead-free solder paste is not as good as lead solder paste in melting point and welding performance, its environmental advantages make it a trend in future electronic manufacturing.
3: The difference in welding performance
Lead solder paste
Lead solder paste has excellent welding performance, and its low melting point makes the welding process easier, and the solder joints are smooth and reliable. Due to its good wettability and fluidity, lead solder paste performs well in the welding of complex circuit boards.
Lead-free solder paste
The melting point of lead-free solder paste is higher, which means that a higher soldering temperature is required, which may increase the thermal stress of components and circuit boards. In addition, the wettability and fluidity of lead-free solder paste are relatively poor, which may cause the solder joints to be less smooth and uniform than those with lead solder paste. However, with the advancement of technology, the soldering performance of lead-free solder paste is also constantly improving.
4: Difference in reliability
Lead solder paste
Due to the good ductility and fatigue resistance of lead alloys, electronic products soldered with lead solder paste have high reliability in long-term use, especially in high-stress environments.
Lead-free solder paste
The mechanical properties of lead-free alloys are relatively poor, but they can still meet the reliability requirements of most electronic products under general use environments. It should be emphasized that for applications requiring high reliability, such as aerospace and medical equipment, it is crucial to select the right lead-free alloy and optimize the soldering process.
Advantages and disadvantages of lead-free and lead solder paste
Advantages and disadvantages of lead-free solder paste1. Environmental protection. Lead solder paste is more harmful to the environment and human body, so many countries and regions have banned the use of lead solder paste.
2. Low temperature resistance. Lead-free solder paste is divided into high temperature, medium temperature and low temperature. Medium temperature and low temperature solder paste can be used for reflow soldering of some components that are not resistant to high temperature. However, low temperature solder paste does not contain silver, and the solder joints will be relatively brittle.
3. Strong activity. Lead-free solder paste is more active than lead solder paste, but its wettability is not as good as that of lead solder paste. Lead-free solder paste can obtain good reflow soldering effect after adjusting the furnace temperature zone line according to its process parameters. Compared with lead solder paste, lead-free solder paste is more difficult to process.
Advantages and disadvantages of lead solder paste
1. It is not environmentally friendly, so the cost is lower, but it is harmful to the environment and human body.
2. Good printing effect. Lead solder paste has strong rolling and tin-dropping properties. During continuous printing, the viscosity changes little, and it still maintains good results for a long time. There is basically no collapse phenomenon, and components are not easy to offset.
3. The reflow soldering effect is good, the solder joints are bright, and the requirements for reflow soldering equipment are not high.
4. There are few residues, which can meet the requirements of no-cleaning and have little corrosion to PCB.
Lead-free solder paste and lead solder paste each have their own advantages and disadvantages. Lead solder paste is known for its excellent welding performance and reliability, but its harm to the environment and health has prompted the development of lead-free solder paste. Lead-free solder paste meets environmental protection requirements. Although it is slightly inferior in some performances, its welding performance and reliability are constantly improving with the advancement of technology. In today's context of environmental protection and health, lead-free solder paste is undoubtedly the future development direction. PCBAMake will select the appropriate solder paste according to the specific application of the customer, and continuously optimize the soldering process to achieve the best soldering effect and reliability.