The impact of DFM on SMT patch processing and its importance
In the field of electronic product manufacturing, surface mount technology (SMT) has become the mainstream assembly technology. Design for manufacturing (DFM), as a method to optimize the design process, has a crucial impact on the quality, efficiency and cost of SMT patch processing.
1. The impact of DFM on SMT patch processing
DFM considers the limitations and optimization of the manufacturing process from the design stage, and its impact on SMT patch processing is mainly reflected in the following aspects:
Improve the yield rate of mounting: DFM reduces interference between components and avoids welding defects by optimizing component layout, pad design, routing rules, etc., thereby improving the yield rate of mounting.
Improve production efficiency: DFM considers the processing capacity of production equipment, optimizes the design to reduce production processes and reduce processing difficulty, thereby improving production efficiency.
Reduce production costs: DFM effectively reduces production costs by reducing design defects, optimizing material use, and improving production efficiency.
Shorten product launch cycle: DFM shortens the time from product design to mass production by reducing design iterations and improving production efficiency, thereby accelerating the product launch cycle.
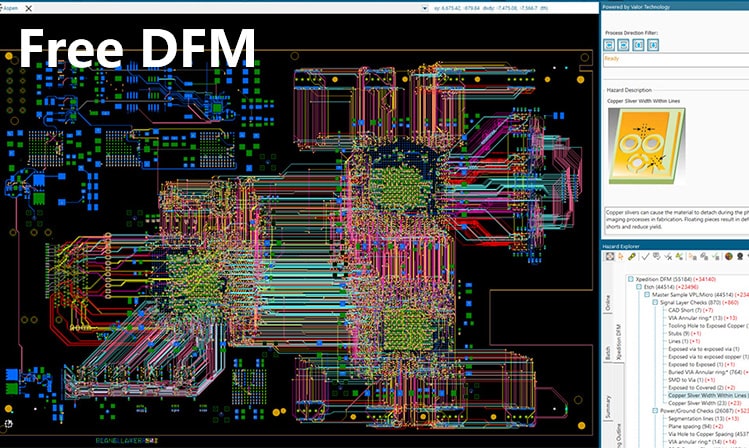
2. The importance of DFM to SMT patch processing
The importance of DFM to SMT patch processing is self-evident, and is mainly reflected in the following aspects:
Ensure product quality: DFM reduces design defects from the source, improves product reliability and stability, and ensures product quality.
Improve corporate competitiveness: DFM helps companies reduce costs, improve efficiency, and shorten cycles, thereby enhancing corporate market competitiveness.
Promote the collaboration of design and manufacturing: DFM emphasizes the collaboration of design and manufacturing, promotes communication between design engineers and manufacturing engineers, and improves product manufacturability.
3. Application of DFM in SMT patch processing
The application of DFM in SMT patch processing runs through the entire design process, mainly including the following aspects:
Component selection: Select components that meet the requirements of SMT process, considering factors such as component packaging, size, and pin spacing.
PCB design: Optimize PCB layout, pad design, routing rules, etc. to meet SMT process requirements.
Stencil design: According to PCB design and component parameters, design a reasonable stencil opening size and shape to ensure solder paste printing quality.
Process parameter setting: According to PCB design, component parameters and solder paste characteristics, set reasonable reflow temperature curve and other process parameters.
DFM is one of the key factors for the success of SMT patch processing. By implementing DFM, product quality can be effectively improved, production costs can be reduced, and product launch cycle can be shortened, thereby enhancing corporate competitiveness. Therefore, companies should attach importance to DFM and integrate it throughout the entire process of product design and manufacturing. Only by integrating the DFM concept into every link of product design and manufacturing can high-quality, low-cost and market-competitive products be produced.