Analysis of the core role and key value of BOM in PCBA processing
In the PCBA processing process, BOM is regarded as the cornerstone of the entire manufacturing process. Whether it is small-batch prototype production or large-scale electronic product manufacturing, the accuracy and completeness of BOM will directly affect the cost, schedule and final quality of the project.
What is BOM?
BOM is one of the core files in the PCBA processing process. It lists in detail all the components, parts, raw materials and their quantities, specifications and parameters required for an electronic product. Simply put, BOM is the "recipe" for product manufacturing, telling manufacturers what "ingredients" are needed and how to "cook".
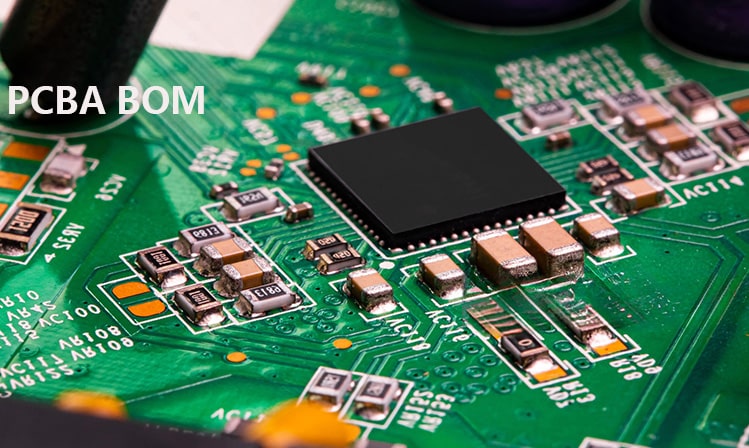
Basic composition of BOM table
A complete PCBA processing BOM table usually contains the following key information:
Component number: unique identifier of each component
Component name: such as resistor, capacitor, IC chip, etc.
Specification parameters: such as resistance value, capacitance value, package form, etc.
Quantity: the number of components used on a single board
Position number: the specific location identification of the component on the PCB board
Manufacturer/brand: recommended or specified supplier information
Alternative material information: alternative component model
Remarks: special requirements or precautions
The core role of BOM table in PCBA processing
1. The cornerstone of production preparation
BOM table is the starting point for PCBA processing plants to prepare for production. Based on the BOM table, the factory can: accurately calculate material requirements, formulate procurement plans, evaluate production costs, and plan production line configurations. Without an accurate BOM table, all subsequent production activities will lose a reliable basis.
2. Compass for material procurement
PCBA processing involves dozens or even hundreds of components. The BOM table provides the procurement department with a clear purchase list to ensure: purchasing the correct component model, purchasing the correct quantity (considering the loss rate), purchasing from the right supplier, and avoiding wrong materials, shortages or insufficient materials.
3. Basis for production process formulation
The component information in the BOM table directly affects the selection of production processes: components of different package types require different mounting processes (SMT, THT, etc.), special components (such as BGA, QFN) require specific welding parameters, and sensitive components (such as electrolytic capacitors) require special processing methods.
4. Important reference for quality control
The BOM table is the basis for the quality department to conduct incoming material inspection (IQC) and production process inspection (IPQC): check whether the actual materials are consistent with the BOM requirements, verify whether the component specifications meet the design requirements, and ensure that the correct materials are used in the production process.
5. Key basis for cost accounting
All material information contained in the BOM is the main basis for calculating PCBA costs: direct material cost accounting, production cost estimation, product pricing reference, and cost optimization analysis.
Key value of the BOM
1. Improve production efficiency
An accurate and complete BOM can significantly improve PCBA processing efficiency: reduce production stoppages caused by material problems, reduce production line change time, improve equipment utilization, and shorten product delivery cycle.
2. Ensure product quality
The BOM guarantees product quality by avoiding the use of unqualified or non-compliant components, ensuring compatibility between components, reducing product defects caused by material errors, and improving product consistency and reliability.
3. Reduce production costs
Cost savings can be achieved by optimizing the BOM: avoid capital occupation caused by excessive procurement, reduce waste caused by material errors, reduce costs through alternative material selection, and optimize inventory management.
4. Promote supply chain collaboration
BOM is the link between design, procurement, production, and supply chain: provide suppliers with clear supply requirements, facilitate multi-factory collaborative production, support global procurement strategies, and improve supply chain response speed.
5. Support product life cycle management
BOM continues to play a role in the product life cycle: design verification in the new product introduction (NPI) stage, production guidance in the mass production stage, maintenance support in the after-sales service stage, and change management of product upgrades and iterations.
How to make a high-quality BOM?
To ensure that the BOM plays the greatest value, it is recommended to follow the following principles:
Accuracy: All information must be accurate, especially key data such as component models and parameters
Integrity: Do not omit any necessary components or information
Consistency: Maintain complete consistency with design documents (such as schematics, PCB diagrams)
Clarity: Use standardized naming and format for easy understanding and use
Traceability: Record version change history for easy tracking and management
Practicality: Consider actual production needs and provide necessary alternative material information, etc.
Common BOM problems and solutions
In actual PCBA processing, BOM is often Problems include:
Incomplete component parameters: Complete specification parameters, especially key parameters
Missing alternative material information: Provide verified alternative material options to enhance supply chain flexibility
Chaotic version management: Establish a strict version control mechanism to ensure the use of the latest version
Inconsistent format: Develop a unified BOM template for the company and standardize filling requirements
Inconsistent with actual design: Regularly check with design documents to ensure consistency
Fully understand the core value of BOM in PCBA processing, and pay more attention to the preparation and management of BOM in actual work, so as to improve product quality and production efficiency and enhance market competitiveness.