What are the advantages and functions of post-soldering process in PCBA processing
Post-soldering process (Post-Soldering) is an important link in PCBA processing. It not only plays an important role in improving the connection strength and stability of the circuit board, but also directly affects the service life and performance of the product
Definition and function of post-soldering process
Post-soldering process refers to the secondary welding operation of some special or vulnerable components after completing the main welding processes such as surface mounting (SMT) and through-hole insertion (DIP). It is usually suitable for high-power components, heat-sensitive components, special-shaped components, and components that may be affected by the soldering temperature of the motherboard.
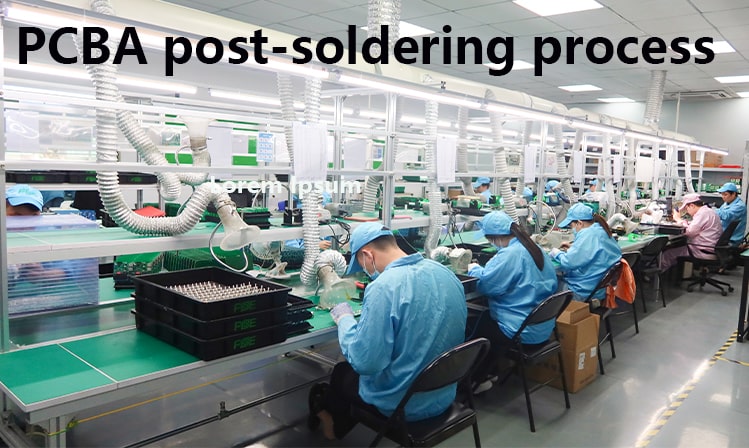
The role of post-soldering process is reflected in the following aspects:
1. Strengthening solder joint connection: For important or high-current carrying devices, post-soldering process can enhance the strength of solder joints to ensure that they will not cause poor contact due to external force or thermal stress during use.
2. Protect sensitive components: Some heat-sensitive components are not suitable for processing in high-temperature reflow soldering or wave soldering. Through post-soldering process, manual soldering or automatic soldering at lower temperatures can be used to ensure the integrity of these components.
3. Improve production flexibility: The post-welding process can be used as a supplementary means, especially when some components need to be adjusted, replaced or repaired. It is more convenient and efficient, which helps to improve the flexibility of the whole board production.
The impact of post-welding process on the quality and stability of PCBA circuit boards
The key to the post-welding process is the fineness and consistency of welding, which has a profound impact on the overall quality and long-term stability of PCBA circuit boards. Through high-quality post-welding process, the reliability of PCBA is greatly improved, which is specifically manifested in the following aspects:
1. Reduce welding defects: In PCBA production, the welding quality directly affects the electrical performance of the circuit board, and problems such as poor contact, cold welding, and cold welding of solder joints will bring safety hazards during use. The post-welding process can effectively repair these defects and ensure the reliability of the overall welding of the circuit board.
2. Enhance seismic performance: Electronic products may encounter external stresses such as vibration or impact in actual use, especially in application scenarios such as automotive electronics and industrial control. The role of post-welding process in strengthening the solder joints of key components can significantly improve the seismic resistance of the circuit board and reduce the risk of solder joint cracking caused by vibration during use.
3. Improve high temperature resistance: For some electronic devices working in high temperature environments (such as automotive electronics and industrial equipment), their PCBA service needs to have strong temperature resistance. The post-welding process provides higher welding strength and stability for special components, enabling them to maintain stable operation in harsh environments.
Case Analysis of the Importance of Post-welding Process
In some high-reliability industries, the post-welding process is particularly important. For example, the ECU (Electronic Control Unit) control unit in the automotive industry has extremely high stability requirements, and even a short-term poor contact may cause a vehicle control system failure. A well-known automobile company once found in actual testing that a key resistor component in its ECU component was loose due to thermal stress. After using the post-welding process to re-reinforce the component, the long-term stability problem was solved and the reliability of the ECU control unit was ensured.
Another typical example is high-power LED lighting products. Due to the high power and large current carrying capacity, common automatic welding cannot provide sufficient solder joint support, resulting in fatigue damage at the welding site, affecting the brightness and life of the LED. The post-welding process provides stronger welding support for such high-power components, greatly extending the life of LED lighting products.
PCBAMake has two post-soldering lines and two plug-in lines to meet your production needs. For more PCBA proofing, PCBA OEM, and PCBA processing knowledge, please contact us at any time.