Visual inspection process flow and role in PCBA processing
In the process of PCBA production, ensuring the stability and consistency of product quality is the top priority in production. As an important part of quality control, visual inspection can quickly discover defects and problems in production, thereby ensuring the final quality of the product.
Visual inspection process flow of SMT production line
The SMT production line is mainly responsible for accurately placing surface mount components on the PCB board and fixing them through reflow soldering. The visual inspection process is usually set at the following key nodes in the SMT PCB production line:
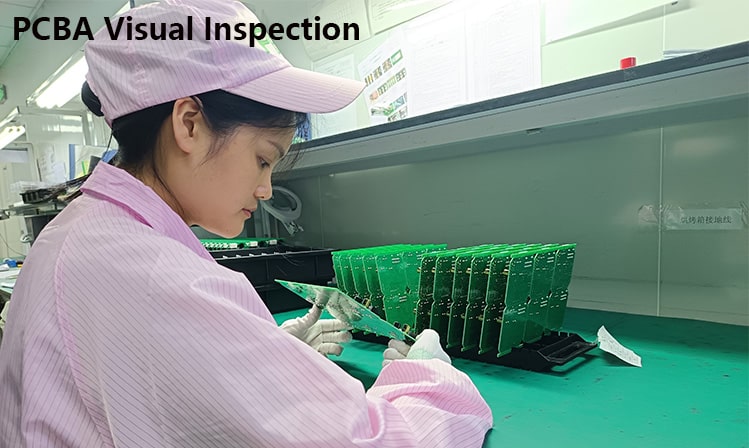
Post-solder paste printing inspection: After the solder paste is printed, a visual inspection is performed to confirm whether the solder paste evenly covers the pad to avoid problems such as a small amount, too much solder paste or printing offset.
Post-chip inspection: After the SMT equipment mounts the component on the PCB board, a manual visual inspection is performed to confirm whether the component has problems such as missing, wrong mounting, offset or flipping. This step is crucial to ensure the correctness of the component.
Post-reflow soldering inspection: After the reflow soldering is completed, a visual inspection is performed to check whether the solder joints are complete, whether the soldering is firm, and whether there are soldering defects such as cold soldering, cold soldering or bridging.
Visual inspection process flow of DIP production line
The DIP production line is used to install larger components on the PCB by plug-in and fix them by wave soldering. The visual inspection process in the DIP production line includes the following steps:
Pre-plug-in inspection: Visual inspection is performed before the components are inserted into the PCB to ensure that the model, specification, polarity, etc. of the components meet the production requirements.
Post-plug-in inspection: After the components are inserted, they are checked before soldering to ensure that the insertion depth and component positioning are correct to avoid wrong insertion or missing insertion.
Post-wave soldering inspection: After wave soldering, visual inspection is performed to confirm whether the solder joints are full, whether there are solder joint voids, tin bridges or cold solder joints, and ensure stable soldering quality
The importance and role of visual inspection
The importance of visual inspection in PCBA production cannot be underestimated. It can not only detect problems in the production process in a timely manner, but also prevent defective products from flowing into the next process, reducing rework and waste. Specifically, visual inspection plays an important role in the following aspects:
Fast detection of defects: Manual visual inspection is highly flexible and can quickly identify subtle problems that may not be detected by the equipment.
Improve product qualification rate: Screen out problematic products through visual inspection to ensure that products that flow into the next process are qualified products.
Save production costs: Timely discovery and correction of problems can reduce the cost of rework and repair and improve overall production efficiency.
Visual inspection is the eternal cornerstone of PCBA quality assurance. In the field of PCBA processing, despite the continuous development of automated inspection technology, the visual inspection process still maintains an irreplaceable position. It is the key embodiment of human experience and judgment in a highly automated production environment, and it is a bridge connecting machine accuracy and product practicality. A rigorous and systematic visual inspection process can not only effectively intercept quality defects, but also provide valuable first-line feedback for process improvement.