Let you know about aluminum PCB
As the electronics industry continues to advance, various electronic products continue to emerge. Among these products, aluminum PCB substrates and PCB boards are two very common substrates, which play key roles in the operation and assembly process of electronic products. However, although the two substrates look similar, they have many significant differences in technology, process and purpose. In the following content, we will compare these two substrates in detail from multiple perspectives.
The following are several types of aluminum substrate PCBs:
Single-sided aluminum PCB: Only one side is attached with circuit board printed circuits, and the other side is pure aluminum or tin-plated. This aluminum substrate is suitable for electronic products that require fewer components and lower power.
Double-sided aluminum PCB: An aluminum substrate with circuit board printed circuits attached to both sides. It can connect circuits on both sides through side holes, blind holes, through holes, etc., and is suitable for electronic products that require more components and higher power.
Thick copper-aluminum PCB: On the ordinary aluminum substrate, after multiple copper platings, thick copper sheets are manufactured. This kind of aluminum substrate has good durability and is suitable for electronic products that require high power, high frequency, and high reliability.
Metal base tape: Aluminum PCB is used as the base material, and the surface is plated with a layer of metal materials, such as copper, silver, nickel, etc. It has the electrical and thermal conductivity properties of metal and the lightness, thinness and high reliability of aluminum substrates. It is widely used in automobiles, aviation and other fields.
Flexible aluminum PCB: Through a special production process, the aluminum PCB is made into a bendable and foldable form. It has excellent thermal properties, corrosion resistance and excellent mechanical strength, and is suitable for mobile communications and other fields.
What are the differences between aluminum PCB and ordinary PCB board:
The substrate is different: the aluminum PCB is made of aluminum as the main material, while the ordinary PCB board is made of copper as the main material.
Different heat dissipation performance: The heat dissipation performance of aluminum substrate is better than that of ordinary PCB board because aluminum has better thermal conductivity.
Prices are different: The price of aluminum substrate is usually higher than that of ordinary PCB board because of its higher production cost.
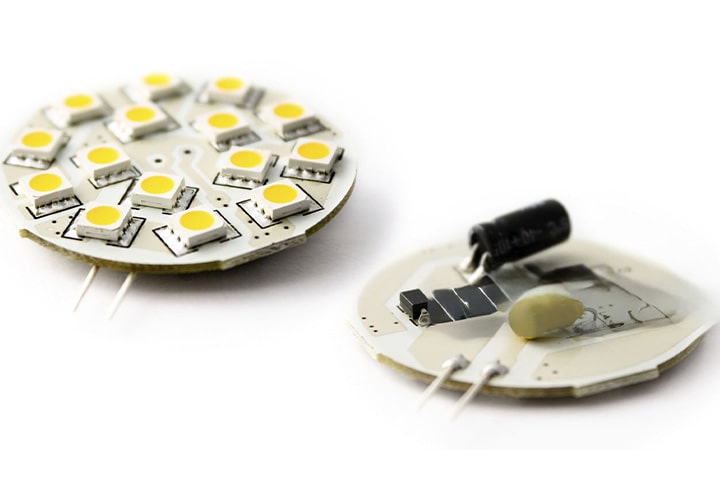
Aluminum substrate PCB has the following advantages:
Good heat dissipation: The aluminum PCB can quickly transfer heat, help the device dissipate heat, reduce thermal resistance, and improve heat dissipation performance.More environmentally friendly: Aluminum PCB do not contain substances harmful to human health and the environment, so they are more environmentally friendly than FR-4 boards.Lightweight: Aluminum PCB base plates have less density and mass, allowing for increased strength and elasticity without adding extra weight.High durability: Compared with FR-4 boards and ceramic substrates, aluminum PCB have higher durability and can avoid warping, bending, cracking, etc. during production and transportation.
Aluminum PCB is mainly used in the following fields:
Audio equipment: used for input (output) amplifiers, balanced amplifiers, audio amplifiers, preamplifiers and power amplifiers, etc.Office automation equipment: used for motor drives, etc.Automobile: used in electronic speed regulators, ignition devices, power controllers, etc.Computer: used for CPU boards, floppy disk drives and power supply equipment, etc.Lamps and lighting: In PCB prototyping, aluminum substrates have also begun to be used in LED lights on a large scale.Aluminum PCB have higher durability than ordinary PCB boards. This is because the aluminum PCB is made of aluminum, which has good thermal conductivity and anti-corrosion properties. It also has strong oxidation resistance, high temperature resistance and anti-corrosion capabilities. Even in harsh environments, aluminum PCB can maintain stable working conditions for a long time, resulting in a longer service life.Aluminum PCB has the following properties:Stability: Aluminum substrates generally have smaller dimensional changes and are more stable than printed boards made of all insulating materials on the market.Insulation: The insulation performance of the aluminum substrate is very good and the hardness is also very high. It can be a good substitute for fragile ceramic plates. This reduces the real area required for the printed board and eliminates the need to install a heat sink on the product, thereby improving the heat dissipation of the product, improving product efficiency and reducing costs.Thermal expansion: The aluminum substrate can improve the heat dissipation function of the product and alleviate the thermal expansion and contraction of components on the printed board, thereby improving the reliability of the product and making the product more durable.Although aluminum PCB and PCB boards look very similar on the surface, there are essential differences between them. Understanding these differences helps us more accurately select the substrate suitable for a specific product, thereby improving product performance, stability and reliability. Regarding the difference between aluminum PCB and PCB board, I will share it here today. If you need to know the details of aluminum PCB, you can click aluminum PCB to view our specific parameters!