Main causes of solder balls during SMT PCBA processing
Surface Mount Technology (SMT) is a widely used process in modern electronic manufacturing. Although SMT improves production efficiency and the performance of electronic products, some problems still occur in actual operation, one of which is the generation of solder balls.
Solder balls not only affect welding quality, but may also cause problems such as short circuits. What are the main causes of solder balls during SMT PCB processing, and the corresponding solutions.
What is solder balls?Tin beads refer to small granular solder that appears on the surface of the PCB or around components after welding during SMT processing. These small granular solders fail to adhere to the solder joints normally, but are scattered around the solder joints or on the surface of the PCB.
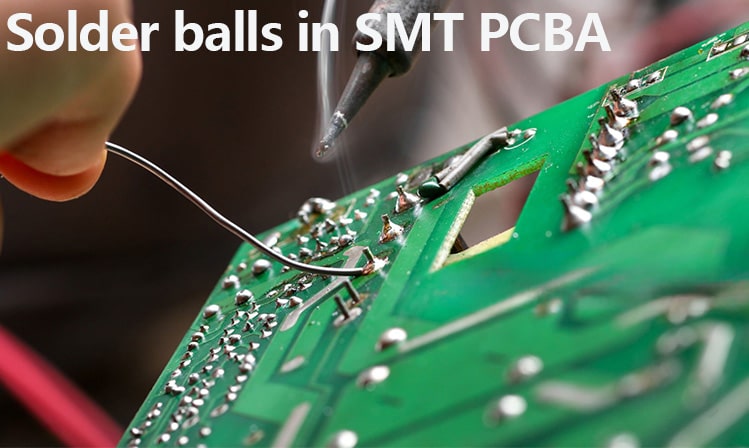
Main causes of solder ballsPoor solder paste printingOverprinting: Too much solder paste is printed, and excess solder paste will overflow from the solder joints during welding, forming solder balls.
Improper steel mesh design: Improper steel mesh opening design may lead to uneven distribution of solder paste and easy generation of solder balls.
Solder paste quality problems: Inappropriate viscosity and particle size of solder paste may lead to uneven printing, thus causing solder balls.
Poor patching
Component position offset: The patch machine is not accurate enough or the programming is wrong, resulting in the components not being accurately mounted on the pads, and the solder paste flows unevenly during welding, forming tin beads.
Excessive patch pressure: Excessive pressure during the patching process causes the solder paste to be squeezed out of the pad area, forming solder balls.
Improper reflow process
Unreasonable heating curve: Improper reflow temperature curve, especially improper preheating and peak temperature control, will cause uneven melting of solder paste and form solder balls.
Oven environment problems: Uneven airflow or excessive pollutants in the reflow oven will also affect the melting and flow of solder paste, resulting in solder balls.
PCB design problems
Unreasonable pad design: Inappropriate pad size or too small spacing can easily lead to uneven distribution of solder paste and solder balls.
Pad surface treatment problems: Oxidation or unevenness of the pad surface affects the adhesion and melting of solder paste and increases the possibility of solder balls.
Prevention and solution measures
Optimize solder paste printing
Adjust printing parameters: Adjust the solder paste printing amount according to actual needs to ensure uniform solder paste thickness.
Improve steel mesh design: Reasonably design the steel mesh opening to ensure uniform distribution of solder paste.
Choose high-quality solder paste: Use suitable solder paste to ensure that its viscosity and particle size meet the process requirements.
Improve patch accuracy
Calibrate the patch machine: Regularly calibrate the patch machine to ensure its accuracy and stability.
Reasonably set the patch pressure: According to the characteristics of components and pads, adjust the patch pressure to avoid excessive pressure causing solder paste extrusion.
Optimize the reflow processReasonably set the heating curve: According to the characteristics of solder paste and components, optimize the reflow heating curve to ensure uniform melting of solder paste.
Keep the soldering furnace clean: Clean the reflow oven regularly to ensure uniform and pollution-free internal airflow.
Reasonably design the pad: According to the specifications of components, design the appropriate pad size and spacing to ensure uniform distribution of solder paste.
Surface treatment: Ensure the quality of the pad surface treatment to avoid oxidation and unevenness.
The generation of tin beads is a common problem in the SMT PCBA processing process, but through reasonable process control and optimized design, the generation of tin beads can be effectively reduced